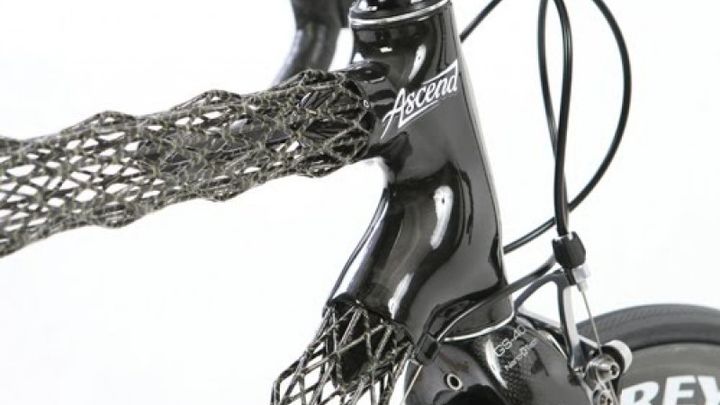
CarbonCoded
Donation protected
Hi kickstart community! I read every day about new and amazing technologies being developed all around the world. What if somebody actually applied them to products people actually wanted to buy and can afford. Enter CarbonCoded, my idea of the future of manufacturing and its application to the transportation industry. Let me tell you a little about this project, who I am, and some of the technology I will be using to be successful.
Project: This campaign is for the first prototype of a scooter called the CS50. It will be the first of its type to allow mass production of lightweight, efficient materials into the structure and building of a scooter. Using the latest advances in technology such as carbon nanotube 3d printing and additive manufacturing techniques we are able to create a product in a far shorter period of time with less waste and more performance than any of the competition. I plan on creating a blog documenting the prototyping process and keeping my backers involved with the kickstarter campaign and the future design of a scooter they can one day purchase. Lightening the frame is only half the project, we plan on using high end aftermarket suspension and a bulletproof 50cc engine with fuel injection for easy starting. Low production car companies already use 3D printing technology to rapidly develop vehicle’s that vastly undercut the auto industry and pave the way for future vehicles to be incredibly light, nimble, and ecofriendly. Much of the waste in producing a vehicle will be trimmed and a smaller engine will be used to propel it into the future, these are our goals.
· Create a rugged futureistic looking scooter that weighs in under 125 pounds
· Use a ubiquitous and proven 50cc engine
· Use the latest in fuel saving technologies such as electric fuel injection
· Carbon fiber or lightweight plastics and metals used throughout chassis
· Open community for prototyping process
· Lightweight wheel design with less rolling mass
· 1500 dollar price point
About: My name is Phillip Malecot and this gofundme is for the upstart of a business I call CarbonCoded. I am an engineer through and through. My father, an aeronautical electrical engineer, and my mother a middle school teacher always taught me to observe the world with a sense of wonder and inquiry. I have always lived this way, when I was five my favorite time of year was fall because the strawberry festival rolled into the local flee market. My favorite thing to do was watch how all the rides moved, my grandmother recounts how I noticed that two of my favorite rides were practically the same followed the same pattern. I have always had a knack for finding patterns, I used this when I started to take things apart and explorer how things worked and were made. Growing up I had the opportunity to own motorcycles and ATVs, and this is where I began cultivating my true passion of learning how things work and the value of working on them myself. My parents bought me my first motorcycle before I could ride my bike and told me that I could ride it when I learned how to ride my bike, it was waiting for me. I soon learned, started riding it, and shortly after crashed into something or other. As I learned to ride I had to learn to repair my motorcycle, my dad showed me and I soon was taking apart all the motorcycles we owned, making sure everything was running and working properly. The further I took things apart the more I understood that they all followed the same underlying principles. As I aged me and my dad’s projects grew more ambitious, we worked on a 93 ford bronco, a green 71 Mach 1 mustang, and a custom built race ready 427 stroked Windsor motor. For me, I've always found value in furthering my education in engineering and its applications to everyday life. Later on, at the begining of my high school career, I would use this knowledge and join the Engineering department. This is where I learned how to use Solidworks and its application to technology and manufacturing. Once I learned the basics I started drafting my own parts and designs testing new ideas as I went. A couple of my designs earned merit but it wasn’t into later that I would apply my CAD skills to the transportation industry. While going to school in Tallahassee I picked up a cheap scooter to replace my daily driver for transportation purposes. I soon started using my scooter for everything, trips to school, the grocery store, they were a breeze with my scooter. This all worked out great until my scooters frame cracked one night coming home with groceries. The scooter nearly fell apart with the whole seat and center portion caving in where I was sitting, I barely made it to the side of the road. I looked at the carnage and thought, this shouldn’t happen, so I went about designing a more rigid chassis in Solidworks, one that is optimized for 3D printing. I eventually came up with a carbon fiber reinforced frame that uses less material and is much stiffer than existing frames. I approach gofundme with an ambitious campaign, let the grassroots movement of crown funding be the wave that enables the common inventor like myself to succeed in making products that undercut traditional big business and enable. I believe the kickstart community is the personification of the American dream manifested in the 21st century, never before has an inventor been able to put themselves out there to a broader spectrum of potential backers, this is CarbonCoded.
Technology: Some of the technology I will be implementing is already in use in the ultra-exclusive high end car companies. They have been using 3D printing technology in their vehicles for several years now with amazing results, but recently there have been upstarts such as the Blade supercar which is about ninety percent 3D printed. Made with its carbon fiber tubular chassis it weighs just 1400 pounds, that’s less than half of already featherweight cars like the Mazda Miata. I want to make this technology obtainable for the general populations. I think the best adaptation of this technology is the scooter industry which is severely outdated. Scooters are relatively cheap to buy, cheap to own, and offer unparalleled flexibility on two wheels. I will bring this lightweight technology to the masses by harnessing the power of 3D printing. By using carbon fibers strength we are able to create a frame and body that is a third of the weight of a regular scooters and design with unparalleled flexibility. Divergent Microfactories is the way manufacturing is moving, a true grassroots movement to let the common inventor create a product that’s not only rigid but also ecofriendly. I believe the best implementation of 3D printing is incorporating it into the existing scooter community. For this prototype I plan on harnessing some of the highest quality, lightest parts I cannot 3d print in carbon and use an existing and proven Honda engine that scooter manufactures use for reliability and robust aftermarket support.
Why weight? Why is reducing weight so important in this project? If we can reduce the weight of the vehicle we can give the rider unparalleled sense of freedom, the scooter will feel light, nimble, and powerful. If we lose weight it is also more ecofriendly with less mass used in production and to push around, we can get by with using smaller engines for better performance and better gas mileage. By using advanced materials such as carbon fiber nanotubes and high resistant plastics we are able to create a design that is extremely lightweight, strong but flexible where we need it.
By keeping the backing community involved in the development and design process we are able to keep everyone satisfied. We can try different ideas based on feedback and rapidly develop a scooter that’s incredibly personable and buyer focused.
Additive manufacturing or rapid prototyping is the next frontier in manufacturing, it is efficient, scalable, and highly versatile. With advancements in 3D printing we are able to cheaply create working prototype parts with unrivaled rigidity and limitless configurations. When my design process is complete I can switch to full scale production using 3D printing. I can simply print the tooling necessary to create the parts at a quicker rate. That’s one of the main points behind additive manufacturing, its growth is exponential.
Future Goals: The future of this project is on Kickstarter, if I can create my prototype and demonstrate the use and versatility of high strength 3D printing, I can persuade others to back CarbonCoded. CarbonCoded is the future of manufacturing demonstrated through personalized cheap transportation. Looking forward I would like to harness the latest in weight saving techniques with a silent electric drivetrain with energy recovery systems and integrated super capacitors to create the ultimate in renewable mobility.
Backing: With your backing I will be able to bring to life my vision of the future of transportation. I will buy a 3D printer capable of printing in the latest materials and start prototyping the parts I’ve already created. As the design process continues I will need more materials to incorporate such as suspension, braking, and engine components. With a 3d scanner the opportunities go further, we can improve upon the engine and suspension components and reduce weight further. Please help me reach my goal, with your backing I will be one step closer to bringing future lightweight materials to the masses. Thanks for all the support!
Videos to watch: https://www.youtube.com/watch?v=Y5wjjDBdgeE
http://3dprint.com/74810/3d-printed-supercar-blade/
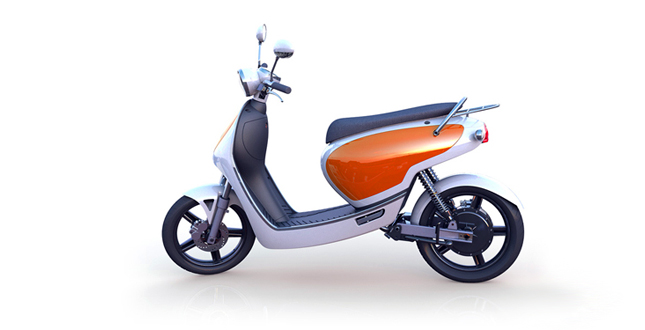
· Create a rugged futureistic looking scooter that weighs in under 125 pounds
· Use a ubiquitous and proven 50cc engine
· Use the latest in fuel saving technologies such as electric fuel injection
· Carbon fiber or lightweight plastics and metals used throughout chassis
· Open community for prototyping process
· Lightweight wheel design with less rolling mass
· 1500 dollar price point
About: My name is Phillip Malecot and this gofundme is for the upstart of a business I call CarbonCoded. I am an engineer through and through. My father, an aeronautical electrical engineer, and my mother a middle school teacher always taught me to observe the world with a sense of wonder and inquiry. I have always lived this way, when I was five my favorite time of year was fall because the strawberry festival rolled into the local flee market. My favorite thing to do was watch how all the rides moved, my grandmother recounts how I noticed that two of my favorite rides were practically the same followed the same pattern. I have always had a knack for finding patterns, I used this when I started to take things apart and explorer how things worked and were made. Growing up I had the opportunity to own motorcycles and ATVs, and this is where I began cultivating my true passion of learning how things work and the value of working on them myself. My parents bought me my first motorcycle before I could ride my bike and told me that I could ride it when I learned how to ride my bike, it was waiting for me. I soon learned, started riding it, and shortly after crashed into something or other. As I learned to ride I had to learn to repair my motorcycle, my dad showed me and I soon was taking apart all the motorcycles we owned, making sure everything was running and working properly. The further I took things apart the more I understood that they all followed the same underlying principles. As I aged me and my dad’s projects grew more ambitious, we worked on a 93 ford bronco, a green 71 Mach 1 mustang, and a custom built race ready 427 stroked Windsor motor. For me, I've always found value in furthering my education in engineering and its applications to everyday life. Later on, at the begining of my high school career, I would use this knowledge and join the Engineering department. This is where I learned how to use Solidworks and its application to technology and manufacturing. Once I learned the basics I started drafting my own parts and designs testing new ideas as I went. A couple of my designs earned merit but it wasn’t into later that I would apply my CAD skills to the transportation industry. While going to school in Tallahassee I picked up a cheap scooter to replace my daily driver for transportation purposes. I soon started using my scooter for everything, trips to school, the grocery store, they were a breeze with my scooter. This all worked out great until my scooters frame cracked one night coming home with groceries. The scooter nearly fell apart with the whole seat and center portion caving in where I was sitting, I barely made it to the side of the road. I looked at the carnage and thought, this shouldn’t happen, so I went about designing a more rigid chassis in Solidworks, one that is optimized for 3D printing. I eventually came up with a carbon fiber reinforced frame that uses less material and is much stiffer than existing frames. I approach gofundme with an ambitious campaign, let the grassroots movement of crown funding be the wave that enables the common inventor like myself to succeed in making products that undercut traditional big business and enable. I believe the kickstart community is the personification of the American dream manifested in the 21st century, never before has an inventor been able to put themselves out there to a broader spectrum of potential backers, this is CarbonCoded.
Technology: Some of the technology I will be implementing is already in use in the ultra-exclusive high end car companies. They have been using 3D printing technology in their vehicles for several years now with amazing results, but recently there have been upstarts such as the Blade supercar which is about ninety percent 3D printed. Made with its carbon fiber tubular chassis it weighs just 1400 pounds, that’s less than half of already featherweight cars like the Mazda Miata. I want to make this technology obtainable for the general populations. I think the best adaptation of this technology is the scooter industry which is severely outdated. Scooters are relatively cheap to buy, cheap to own, and offer unparalleled flexibility on two wheels. I will bring this lightweight technology to the masses by harnessing the power of 3D printing. By using carbon fibers strength we are able to create a frame and body that is a third of the weight of a regular scooters and design with unparalleled flexibility. Divergent Microfactories is the way manufacturing is moving, a true grassroots movement to let the common inventor create a product that’s not only rigid but also ecofriendly. I believe the best implementation of 3D printing is incorporating it into the existing scooter community. For this prototype I plan on harnessing some of the highest quality, lightest parts I cannot 3d print in carbon and use an existing and proven Honda engine that scooter manufactures use for reliability and robust aftermarket support.
Why weight? Why is reducing weight so important in this project? If we can reduce the weight of the vehicle we can give the rider unparalleled sense of freedom, the scooter will feel light, nimble, and powerful. If we lose weight it is also more ecofriendly with less mass used in production and to push around, we can get by with using smaller engines for better performance and better gas mileage. By using advanced materials such as carbon fiber nanotubes and high resistant plastics we are able to create a design that is extremely lightweight, strong but flexible where we need it.
By keeping the backing community involved in the development and design process we are able to keep everyone satisfied. We can try different ideas based on feedback and rapidly develop a scooter that’s incredibly personable and buyer focused.
Additive manufacturing or rapid prototyping is the next frontier in manufacturing, it is efficient, scalable, and highly versatile. With advancements in 3D printing we are able to cheaply create working prototype parts with unrivaled rigidity and limitless configurations. When my design process is complete I can switch to full scale production using 3D printing. I can simply print the tooling necessary to create the parts at a quicker rate. That’s one of the main points behind additive manufacturing, its growth is exponential.
Future Goals: The future of this project is on Kickstarter, if I can create my prototype and demonstrate the use and versatility of high strength 3D printing, I can persuade others to back CarbonCoded. CarbonCoded is the future of manufacturing demonstrated through personalized cheap transportation. Looking forward I would like to harness the latest in weight saving techniques with a silent electric drivetrain with energy recovery systems and integrated super capacitors to create the ultimate in renewable mobility.
Backing: With your backing I will be able to bring to life my vision of the future of transportation. I will buy a 3D printer capable of printing in the latest materials and start prototyping the parts I’ve already created. As the design process continues I will need more materials to incorporate such as suspension, braking, and engine components. With a 3d scanner the opportunities go further, we can improve upon the engine and suspension components and reduce weight further. Please help me reach my goal, with your backing I will be one step closer to bringing future lightweight materials to the masses. Thanks for all the support!
Videos to watch: https://www.youtube.com/watch?v=Y5wjjDBdgeE
http://3dprint.com/74810/3d-printed-supercar-blade/
Organizer
Phillip Malecot
Organizer
Tallahassee, FL