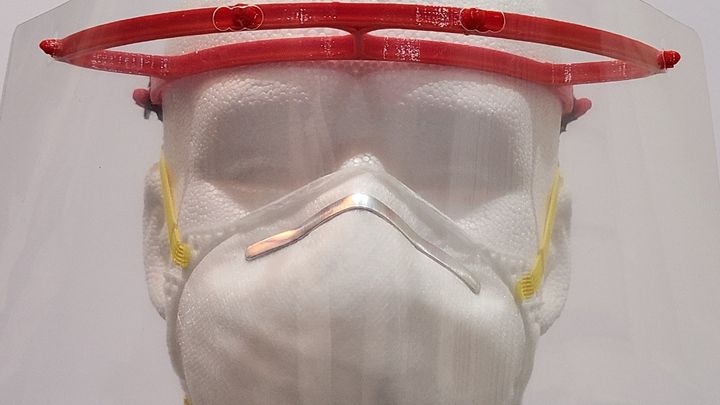
Community Sourced Face Shield
Donation protected
We are raising money to produce face shields for Boston-area hospitals in support of COVID-19 response. The key challenge is bottlenecks in traditional supply chains make it nearly impossible to get critical PPE items to hospitals.
Living in Boston, I have heard a few friends who work as nurses and doctors at various hospitals in the area put requests out through social media for PPE. It came as a suprise to me how quickly our supply chains could be overwhelmed by a pandemic response. I looked for myself and saw many face shield and mask suppliers were backordered for 6-8 weeks. Not only that, but as a medical device designer, I was seeing backlogs from my own suppliers even for the raw materials of these types of products (namely filter fabric, strapping, and plastic sheeting).
The thought that good friends of mine are going to work on the front lines unprotected is terrible! My wife is a nurse, my mother is a nurse. I can't imagine sending them into this type of environment.
This project is motivated by a desire to protect friends and family, and do whatever I can to contribute and support the community while contained in the confines of my home office and company labs.
Recognizing that this is a supply chain issue, my goal for this project is to provide and donate face shields using 100% locally available materials. I assembled a team of engineers willing to donate their time, and we have prototyped our first 150 face shields through the use of my 3D printer and some off-the-shelf office supplies with great success!
I would now like to scale our volunteer network to supply more donated face shields to Boston area hospitals in advance of rising needs. These are strictly for emergency use as a "last resort" solution in the event traditional supplies are overwhelmed and non-existent.
To this end, as director of product development at a Boston medical device company, I was able to pull together a stellar team of engineers to solve this problem. Within 2 days we had design concepts and prototype materials ordered. Within 1 week we had two designs built and submitted to a local hospital for evaluation. We feel these two designs, in concert, provide us with great flexibliity in producing face shields in a world where inventory in typical supply routes is non-existent.
The two designs we will leverage to produce face shields are described below. Depending on availability of supplies, we can better hedge our risk of supply bottlenecks amidst this rapidly changing supply chain by pivoting to either of these designs:
Design 1: The arista Frame Design
FIG 1. Exploded assembly view of the arista face shield design shows the basic design construction.
FIG 2. Photo showing lamination of a 5 mil lamination pouch, sourced from a local office supply store. These can be run through a laminator empty. They are then trimmed and punched to assemble to a 3D printed frame.
FIG 3. Photo of the arista face shields assembled prior to being decontaminated with isopropoanol and immediately sealed into polyethylene bags.
FIG 4. Bagged arista face shields, prior to labeling and binning into polypropylene tubs.
The arista frame design relies on a 3D printed frame and 5 mil PET laminating pouches. This frame has been designed with inspiration from the PRUSA open-sourced frame, but with the goal of reducing print time down to under 1hr and improving ergonomics. This design is faster to produce and I have made my design open source for anyone who would like to duplicate my efforts. You can download these files for free from my grabcad site here: https://grabcad.com/library/arista-face-shield-1
The obvious limitation of this design is the speed of printing frames. However with crowd-sourced printing and local companies in the area contributing to the cause, it is surprising how many can be produced quickly! We will also serve as a hub to hobbyist printers willing to print and ship these frames to our donated office space.
We have a second design that is frameless and gets around the bottleneck of 3D printed frames. However, the design tradeoff here is that this requires foam sourced from local hardware stores. and PVC binder covers sourced from office supply stores. The foam does not hold the shield quite as far from the face as the 3D print, but this may not be concern. The plastic rivets and elastic are the only online-purchased component which are relatively ubiquitous and could be swapped for other locally-sourced straps and fasteners.
Design 2: The Frameless Design
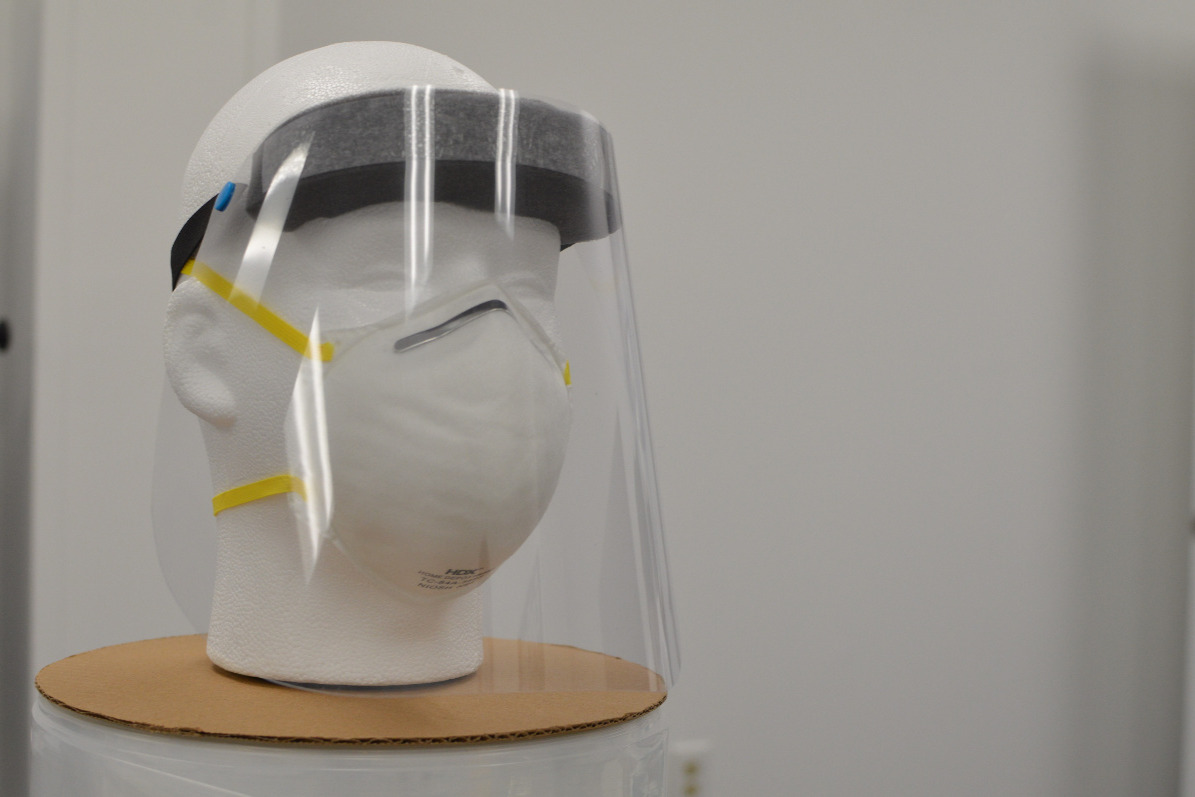
FIG 5. Photo of frameless face shield (top) and work in progress foam (bottom).
Assembly and Packaging
We assemble all face shields with a team of engineers in donated office space (thanks to my full-time gig). We wear PPE (N95 respirator, lab coat, gloves, and goggles), and make our best attempt to sanitize each 3D print by soaking it in 95% isopropanol prior to assembly, and then a final wipe of each shield with 95% isopropanol after assembly, just prior to sealing them in a 8mil polyethylene bag. We then drive and deliver these shields for donation to our friends at local Boston area hospitals where they are recieved and put through decontamination protocols prior to evaluation.
FIG 6. Photograph of finished and packaged community-built face shields.
Disclaimer
We also assure that hospitals understand that these shields are 100% donated, community made, and are provided for evaluation purposes only. Although we want them to help our loved ones, we recognize that these are not validated face shields, and carry with them no gurantees or claims to be adequate PPE. They may not work!
Budget
An estimate of the costs is shown below
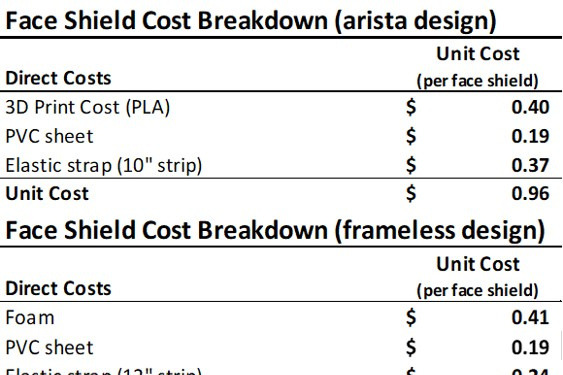
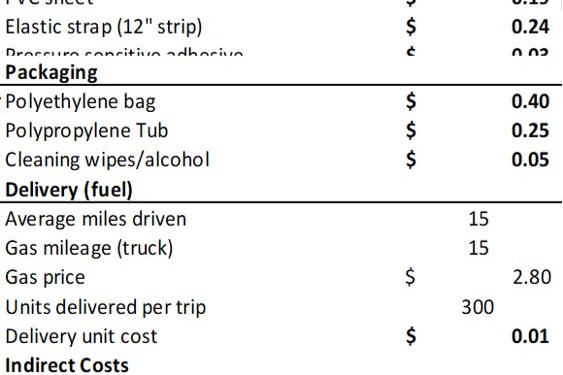
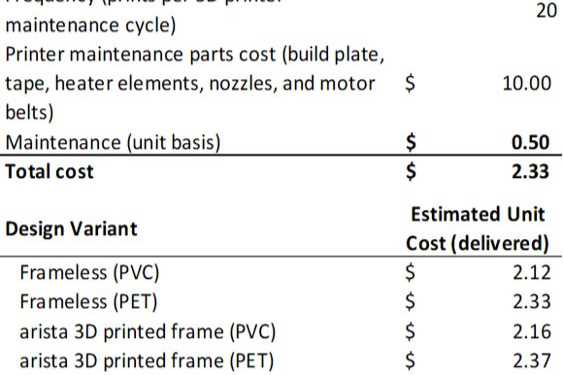
Depending on our production route we will expect a delivered cost of $2.12 to $2.37 per face shield. These costs of course do not take into account overhead of our facility and personnel hours. These expenses will be donated by volunteers and my full-time employer has opened its doors to us to conduct builds.
Your donations will go to direct production and delivery costs of these face shields. If we exceed our goal we will allocate funds to increase our efficiency by purchasing some eqiupment that will speed up assembly, including a rotary die cutter, 3D printers, fixtures, jigs, and laminating supplies.
Our goal is to produce 2,000 shields for donation to local hospitals within 2 weeks of reaching the goal and we will continue the operation as long as we can until traditional supply chains are restored.
Thank you in advance for your support.
Living in Boston, I have heard a few friends who work as nurses and doctors at various hospitals in the area put requests out through social media for PPE. It came as a suprise to me how quickly our supply chains could be overwhelmed by a pandemic response. I looked for myself and saw many face shield and mask suppliers were backordered for 6-8 weeks. Not only that, but as a medical device designer, I was seeing backlogs from my own suppliers even for the raw materials of these types of products (namely filter fabric, strapping, and plastic sheeting).
The thought that good friends of mine are going to work on the front lines unprotected is terrible! My wife is a nurse, my mother is a nurse. I can't imagine sending them into this type of environment.
This project is motivated by a desire to protect friends and family, and do whatever I can to contribute and support the community while contained in the confines of my home office and company labs.
Recognizing that this is a supply chain issue, my goal for this project is to provide and donate face shields using 100% locally available materials. I assembled a team of engineers willing to donate their time, and we have prototyped our first 150 face shields through the use of my 3D printer and some off-the-shelf office supplies with great success!
I would now like to scale our volunteer network to supply more donated face shields to Boston area hospitals in advance of rising needs. These are strictly for emergency use as a "last resort" solution in the event traditional supplies are overwhelmed and non-existent.
To this end, as director of product development at a Boston medical device company, I was able to pull together a stellar team of engineers to solve this problem. Within 2 days we had design concepts and prototype materials ordered. Within 1 week we had two designs built and submitted to a local hospital for evaluation. We feel these two designs, in concert, provide us with great flexibliity in producing face shields in a world where inventory in typical supply routes is non-existent.
The two designs we will leverage to produce face shields are described below. Depending on availability of supplies, we can better hedge our risk of supply bottlenecks amidst this rapidly changing supply chain by pivoting to either of these designs:
Design 1: The arista Frame Design
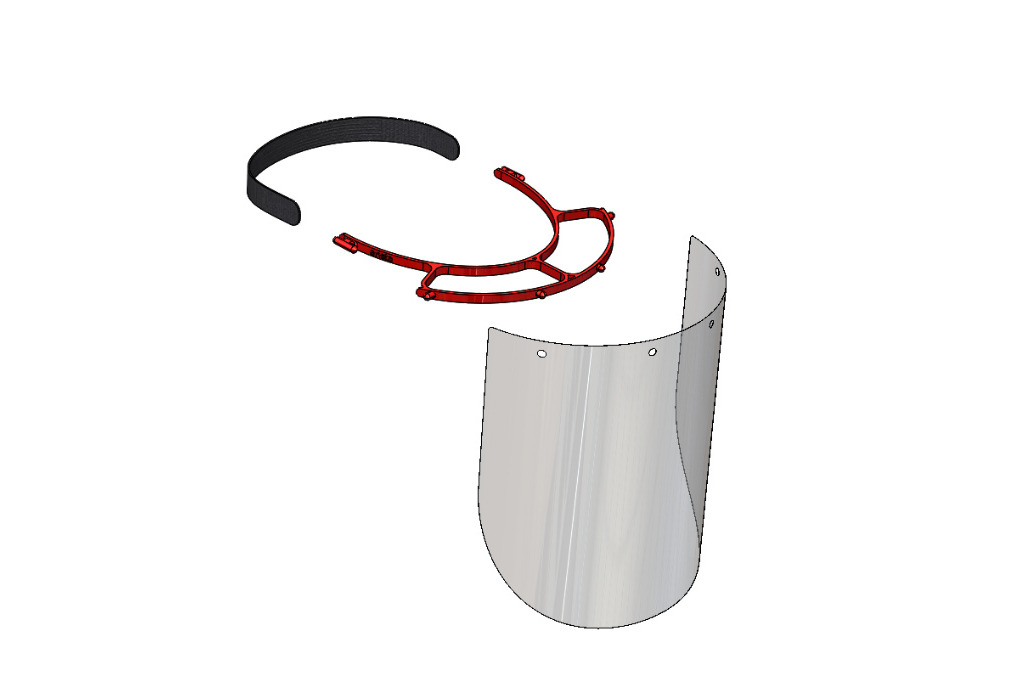
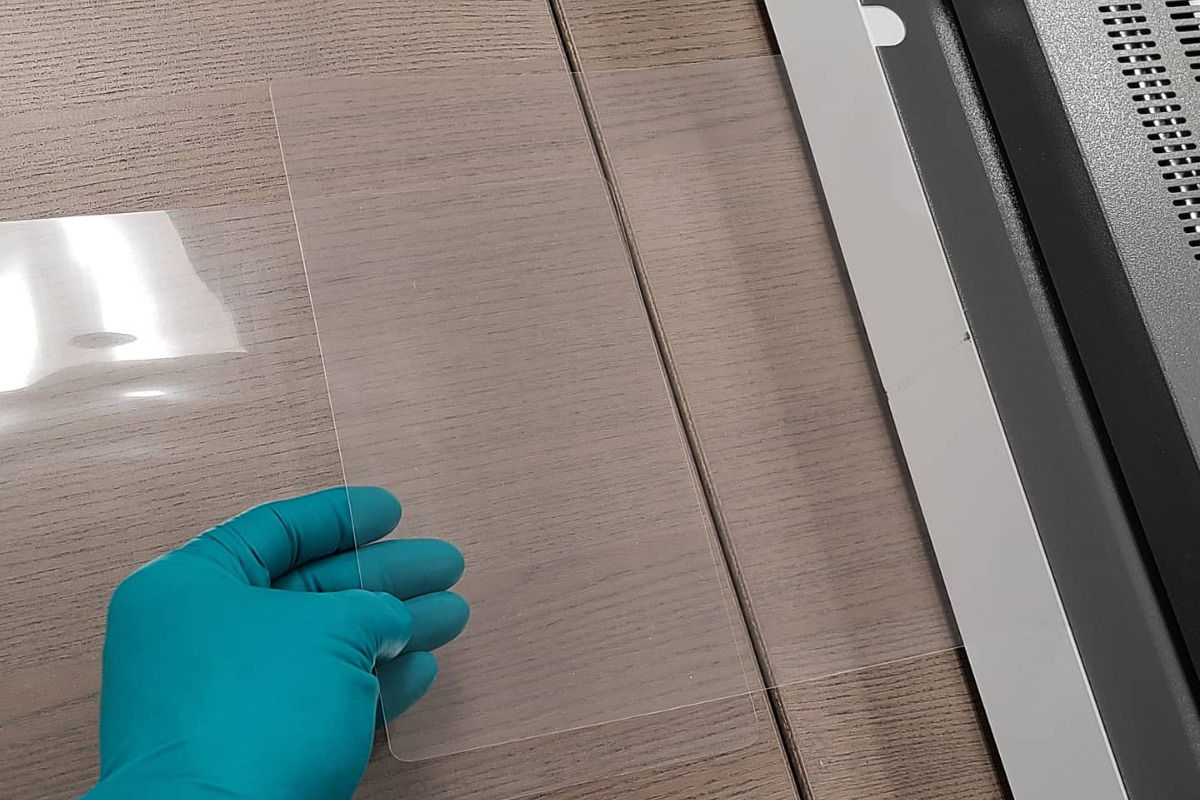
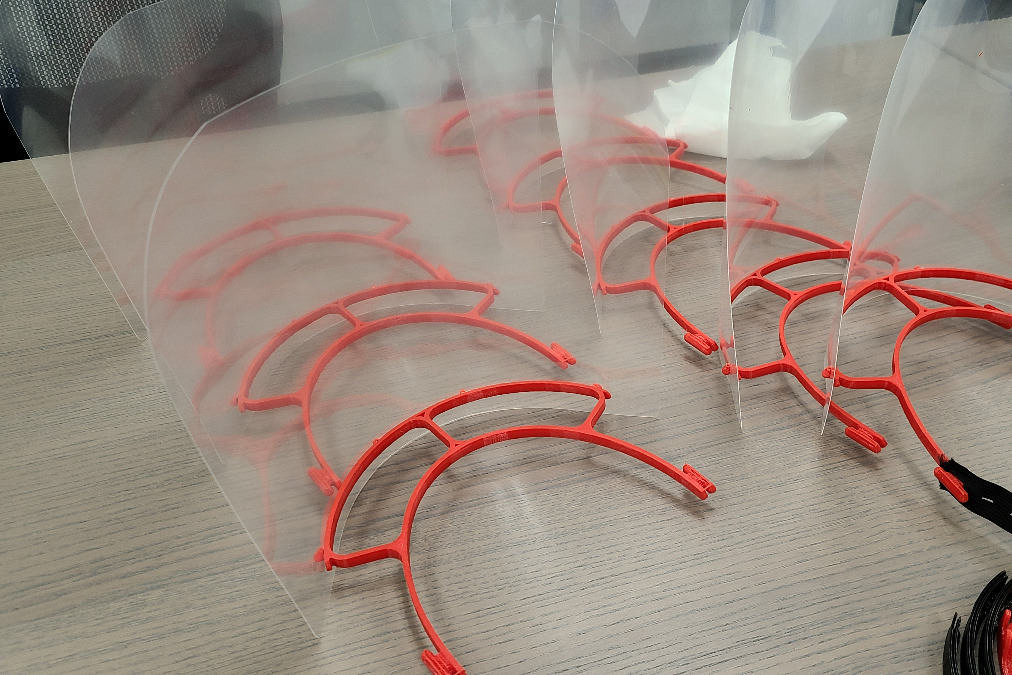
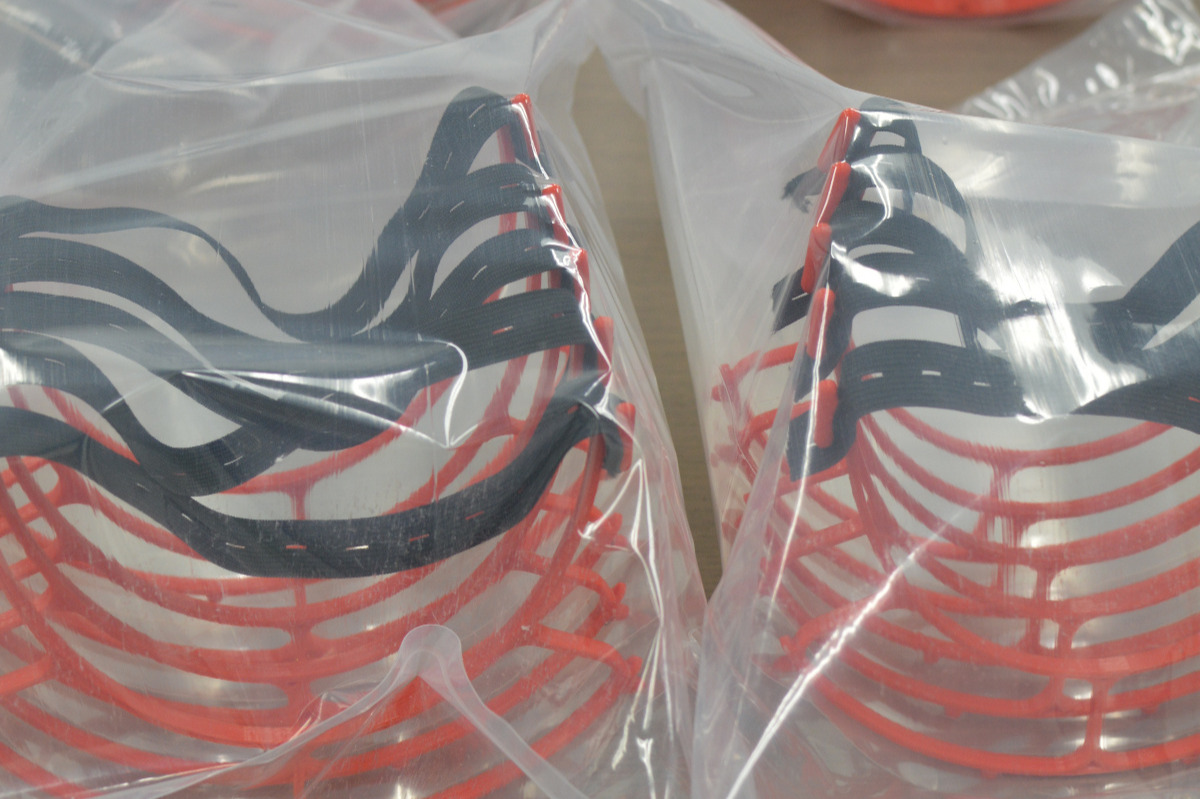
The arista frame design relies on a 3D printed frame and 5 mil PET laminating pouches. This frame has been designed with inspiration from the PRUSA open-sourced frame, but with the goal of reducing print time down to under 1hr and improving ergonomics. This design is faster to produce and I have made my design open source for anyone who would like to duplicate my efforts. You can download these files for free from my grabcad site here: https://grabcad.com/library/arista-face-shield-1
The obvious limitation of this design is the speed of printing frames. However with crowd-sourced printing and local companies in the area contributing to the cause, it is surprising how many can be produced quickly! We will also serve as a hub to hobbyist printers willing to print and ship these frames to our donated office space.
We have a second design that is frameless and gets around the bottleneck of 3D printed frames. However, the design tradeoff here is that this requires foam sourced from local hardware stores. and PVC binder covers sourced from office supply stores. The foam does not hold the shield quite as far from the face as the 3D print, but this may not be concern. The plastic rivets and elastic are the only online-purchased component which are relatively ubiquitous and could be swapped for other locally-sourced straps and fasteners.
Design 2: The Frameless Design
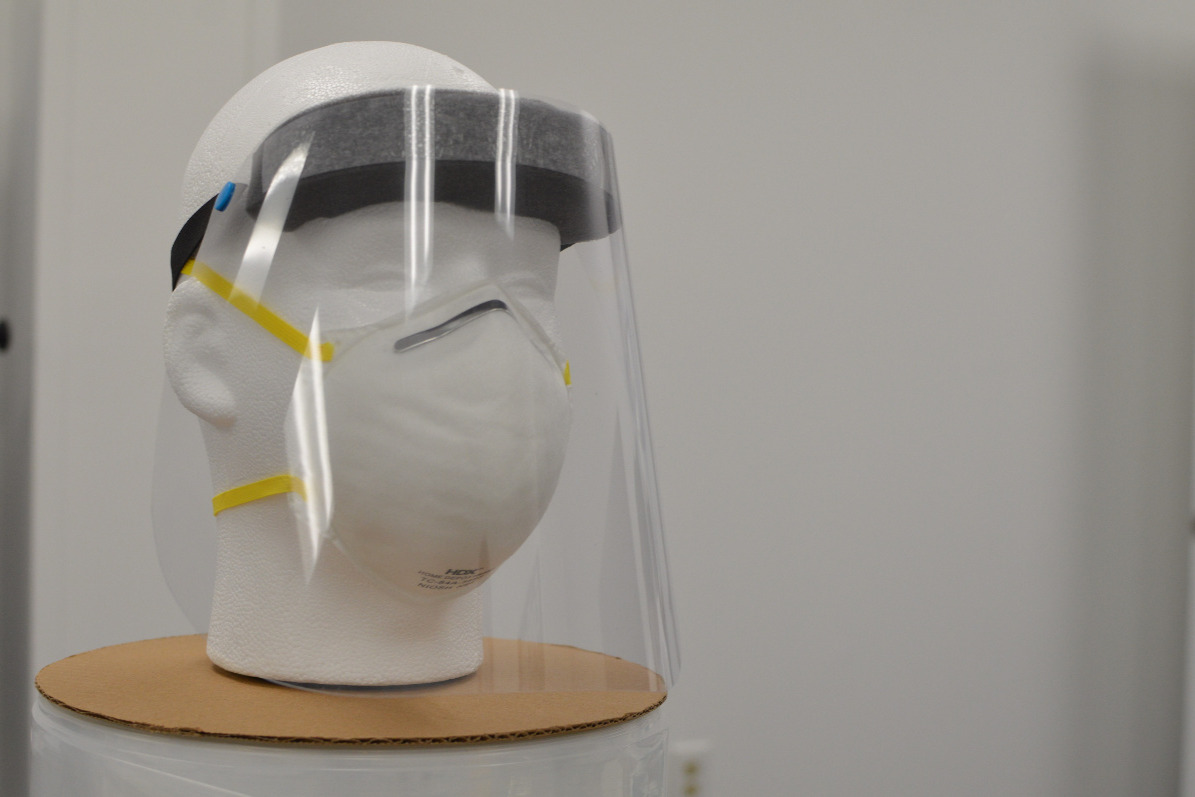
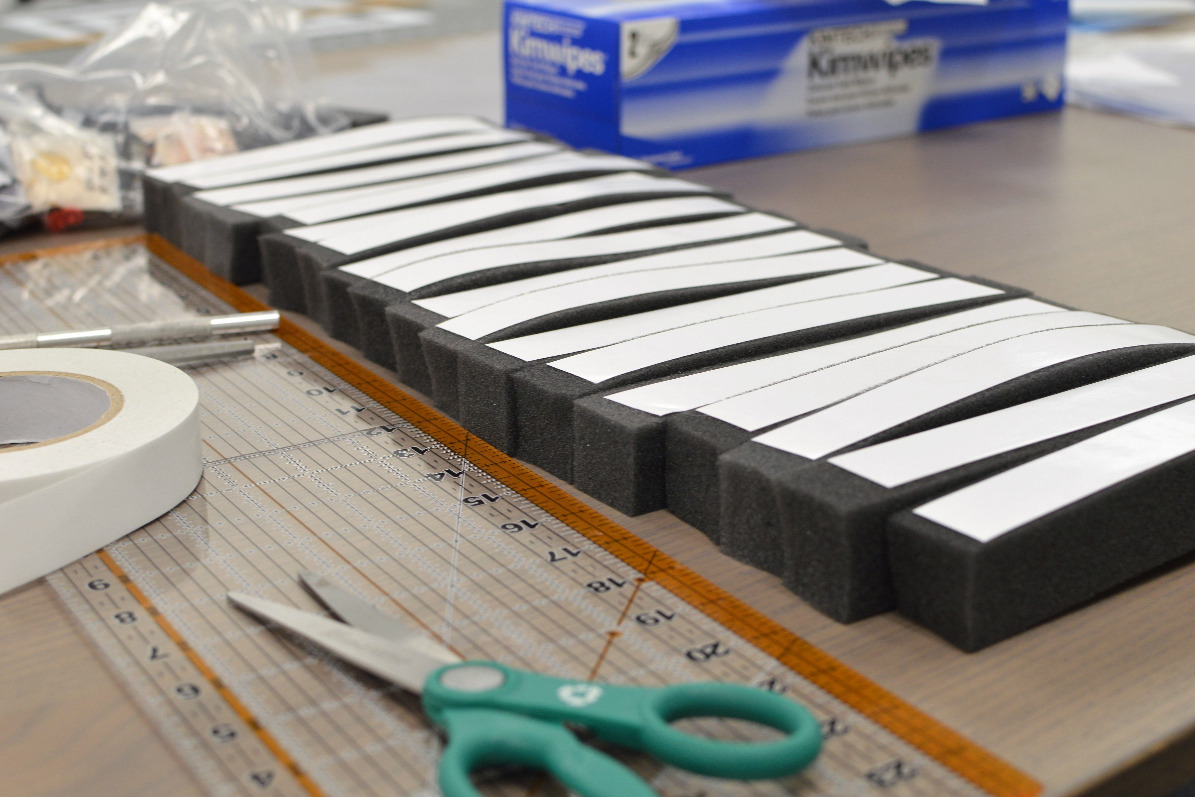
Assembly and Packaging
We assemble all face shields with a team of engineers in donated office space (thanks to my full-time gig). We wear PPE (N95 respirator, lab coat, gloves, and goggles), and make our best attempt to sanitize each 3D print by soaking it in 95% isopropanol prior to assembly, and then a final wipe of each shield with 95% isopropanol after assembly, just prior to sealing them in a 8mil polyethylene bag. We then drive and deliver these shields for donation to our friends at local Boston area hospitals where they are recieved and put through decontamination protocols prior to evaluation.
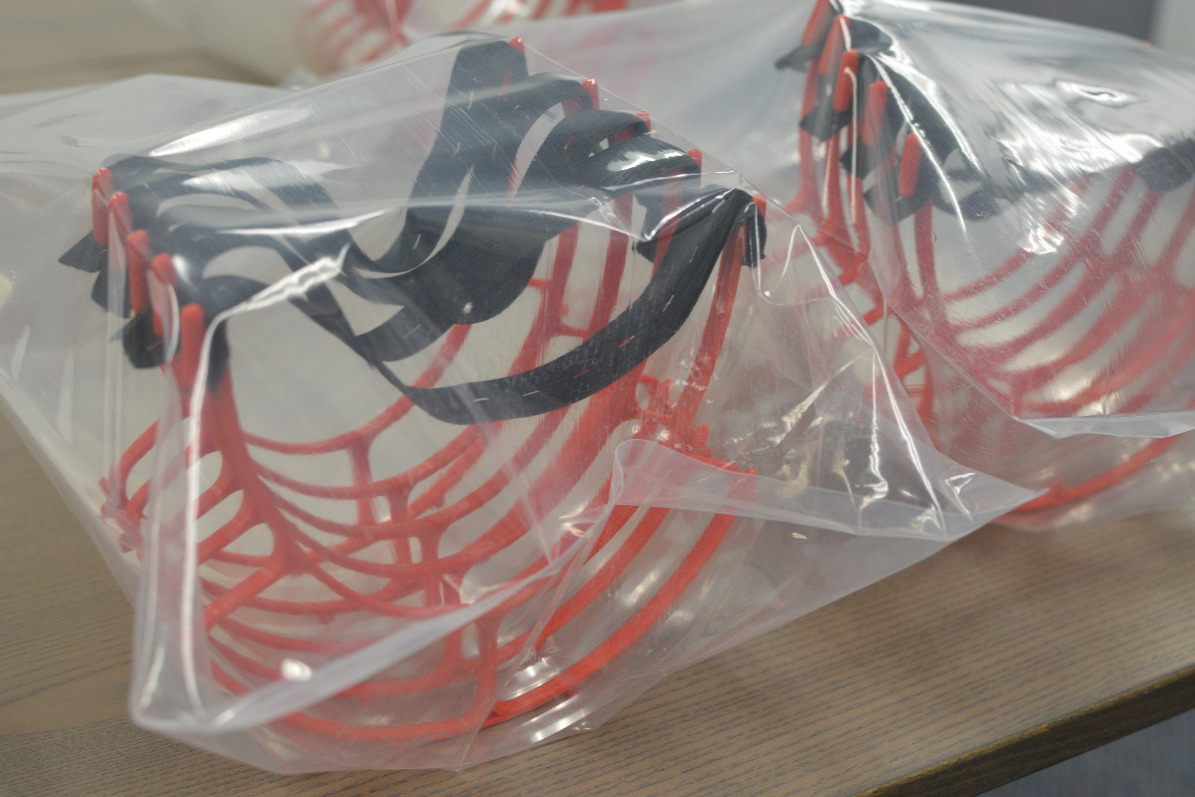
Disclaimer
We also assure that hospitals understand that these shields are 100% donated, community made, and are provided for evaluation purposes only. Although we want them to help our loved ones, we recognize that these are not validated face shields, and carry with them no gurantees or claims to be adequate PPE. They may not work!
Budget
An estimate of the costs is shown below
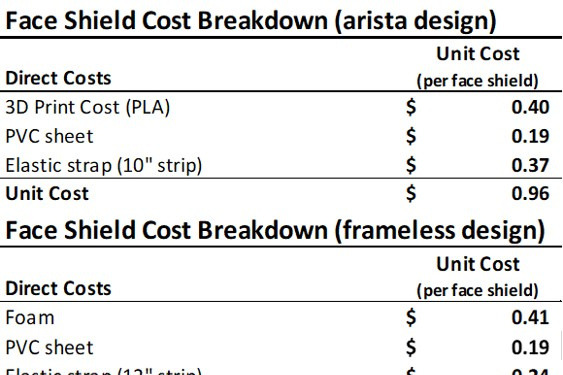
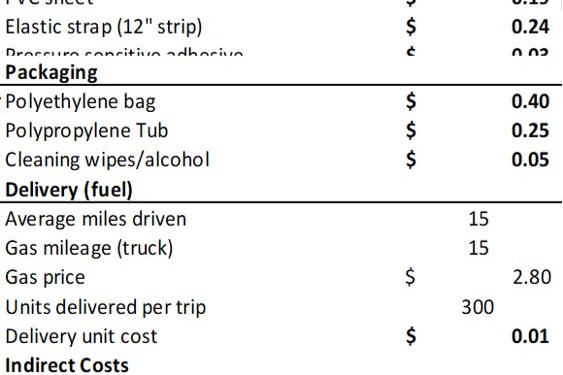
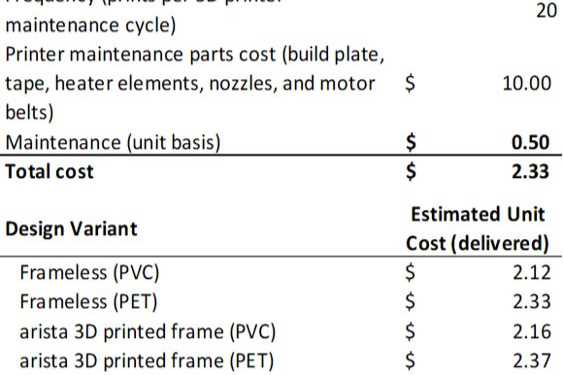
Depending on our production route we will expect a delivered cost of $2.12 to $2.37 per face shield. These costs of course do not take into account overhead of our facility and personnel hours. These expenses will be donated by volunteers and my full-time employer has opened its doors to us to conduct builds.
Your donations will go to direct production and delivery costs of these face shields. If we exceed our goal we will allocate funds to increase our efficiency by purchasing some eqiupment that will speed up assembly, including a rotary die cutter, 3D printers, fixtures, jigs, and laminating supplies.
Our goal is to produce 2,000 shields for donation to local hospitals within 2 weeks of reaching the goal and we will continue the operation as long as we can until traditional supply chains are restored.
Thank you in advance for your support.
Organizer
Adam Standley
Organizer
Watertown, MA